Soft ore offers Sarytogan big savings at Kazakh graphite project
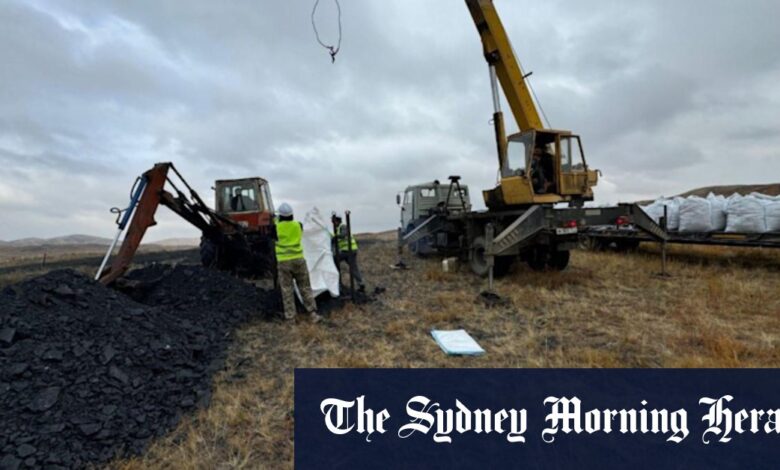
The metallurgical test work was conducted by the LLP Kazidromed laboratory, based in the nearby regional capital Karaganda, under the supervision of the Australian comminuction expert Dean David.
The milling involved a 78 cm 78 cm sphere mill in closed circuit using a hydrocyclone to separate solid particles according to their size and density from a liquid flow. The power demand was measured during the execution of the unpaid without load and during each test of grinding and measurements of the dimensions were acquired at the end of each key test phase.
The initial tests at a 300 kilograms at a time per hour, 500 kg/hour, 700 kg/hour and 800 kg/now have shown a speed of progress of the pilot mill at 317 kg/h is optimal to obtain a target sizing of 95 % which passes 106 micron (0.106 mm).
That initial test phase was followed by milling runs at the speed of 317 kg/h optimal to determine a definitive operational operating work index for the project.
The 6.05 kilowatt index for tonnata confirmed that the mineral is very soft and considerably softer than all previous hypotheses.
Sean Gregory, CEO of Sardin Graphite, said: “This pilot -scale milling test has shown the low grinding costs of our very soft graphite Sartogan mineral. It highlights one of the main strategic advantages of SARYTOGAN; be able to go directly to a fine microcrystalline graphite without being encouraged expensively.
Sardeogan sees the operational working index for his graphite from his wet milling on a pilot scale as a more reliable measure of hardness and comparative macinity of the mineral.
He says that the alternative of dry milling could result in adhesion to graphite and the coating of a surface of the grinding vehicle, which would reduce the effectiveness of the mill and would lead to distorted results. Dry milling could also blind the product sizing screens used for tests.
The impressive results of wet milling will flow on significant savings in the shattering requirements and eliminate the need for jaw mills and cone from the initial preface study study, allowing Serarytogan to replace the equipment with lighter units such as the dental mills.
The last test of the 317 kg/h test suggests that Serarytogan can use a much smaller sphere mill with an installed motor power of about 175 kilowatt and a net power of 150 kW, equal to 65 % and 36 % respectively compared to the pre-capacity study of the company.
Other significant savings on costs include reduced maintenance due to the reduced wear of the components and less risks that reach the optimal use of the grinding circuit.
Serarytogan can optimize the preparation for the power supply of the mills, properly adapting the equipment to the soft mineral, bringing to better performance downstream, greater productivity and reduced inactivity times.
The company plans to send about 700 kg of the ground mineral to Australia to generate more concentrate of in bulk fleet. In 2023, the company treated a 60 kg sample in the same way to produce 20 kg of concentrate.
The previous test work has reached a degree of concentrate of 81.4 percent of TGC to 84.4 percent recovery from a composite sample representative from eight perforation holes diamond by the areas of northern and central graphite of the project with a degree of head of 32.5 percent.
After completing the floating test work, the final concentrate samples will be available for the supplier test work using equipment designed for thermal purification, classification of size and spheronization. Even more important, the final work will also produce champions that SarnytoGan can send to its customers.
Is your company listed in Asx doing something interesting? Contact: matebirney@bullsnbears.com.au